The 7-Second Trick For Alcast Company
Table of ContentsWhat Does Alcast Company Do?Rumored Buzz on Alcast CompanyThe Basic Principles Of Alcast Company What Does Alcast Company Do?Facts About Alcast Company RevealedExcitement About Alcast Company
The subtle difference lies in the chemical content. Chemical Comparison of Cast Aluminum Alloys Silicon advertises castability by reducing the alloy's melting temperature level and improving fluidity during spreading. It plays an essential role in enabling intricate molds to be filled up accurately. In addition, silicon adds to the alloy's strength and wear resistance, making it beneficial in applications where toughness is essential, such as vehicle parts and engine elements.It likewise improves the machinability of the alloy, making it much easier to refine right into finished products. In this means, iron contributes to the general workability of light weight aluminum alloys.
Manganese adds to the stamina of aluminum alloys and boosts workability (Aluminum Castings). It is frequently made use of in functioned aluminum products like sheets, extrusions, and profiles. The presence of manganese aids in the alloy's formability and resistance to cracking during fabrication processes. Magnesium is a light-weight aspect that offers toughness and influence resistance to aluminum alloys.
Get This Report about Alcast Company
Zinc improves the castability of light weight aluminum alloys and assists regulate the solidification procedure during spreading. It enhances the alloy's stamina and firmness.
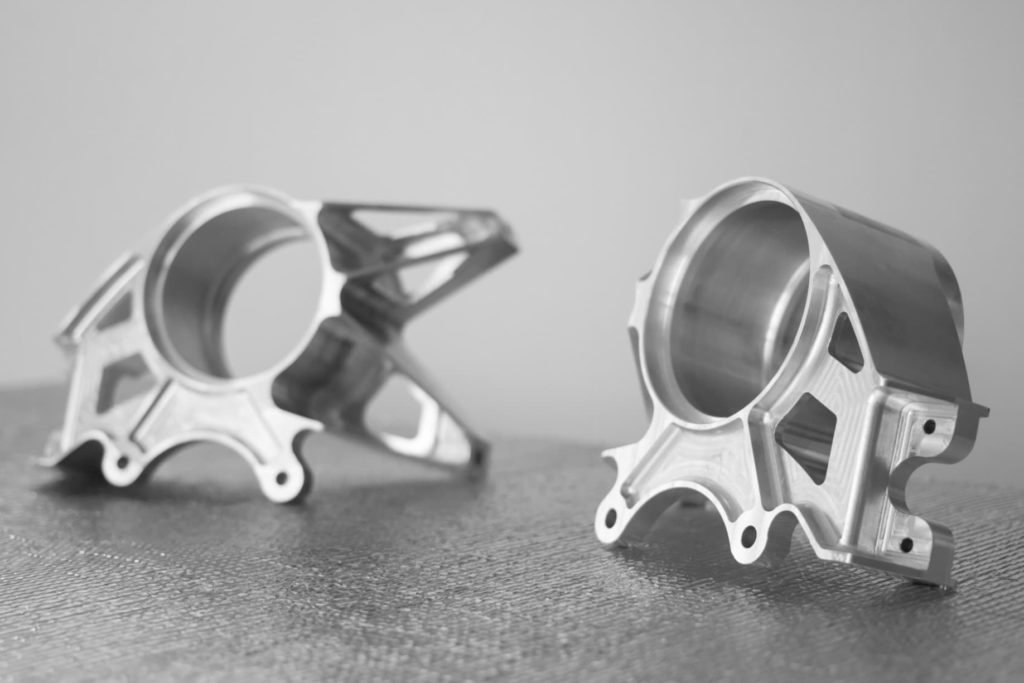
The main thermal conductivity, tensile toughness, yield strength, and elongation vary. Select ideal basic materials according to the performance of the target product produced. Amongst the above alloys, A356 has the highest possible thermal conductivity, and A380 and ADC12 have the lowest. The tensile limit is the opposite. A360 has the very best yield toughness and the greatest elongation rate.
Our Alcast Company Ideas
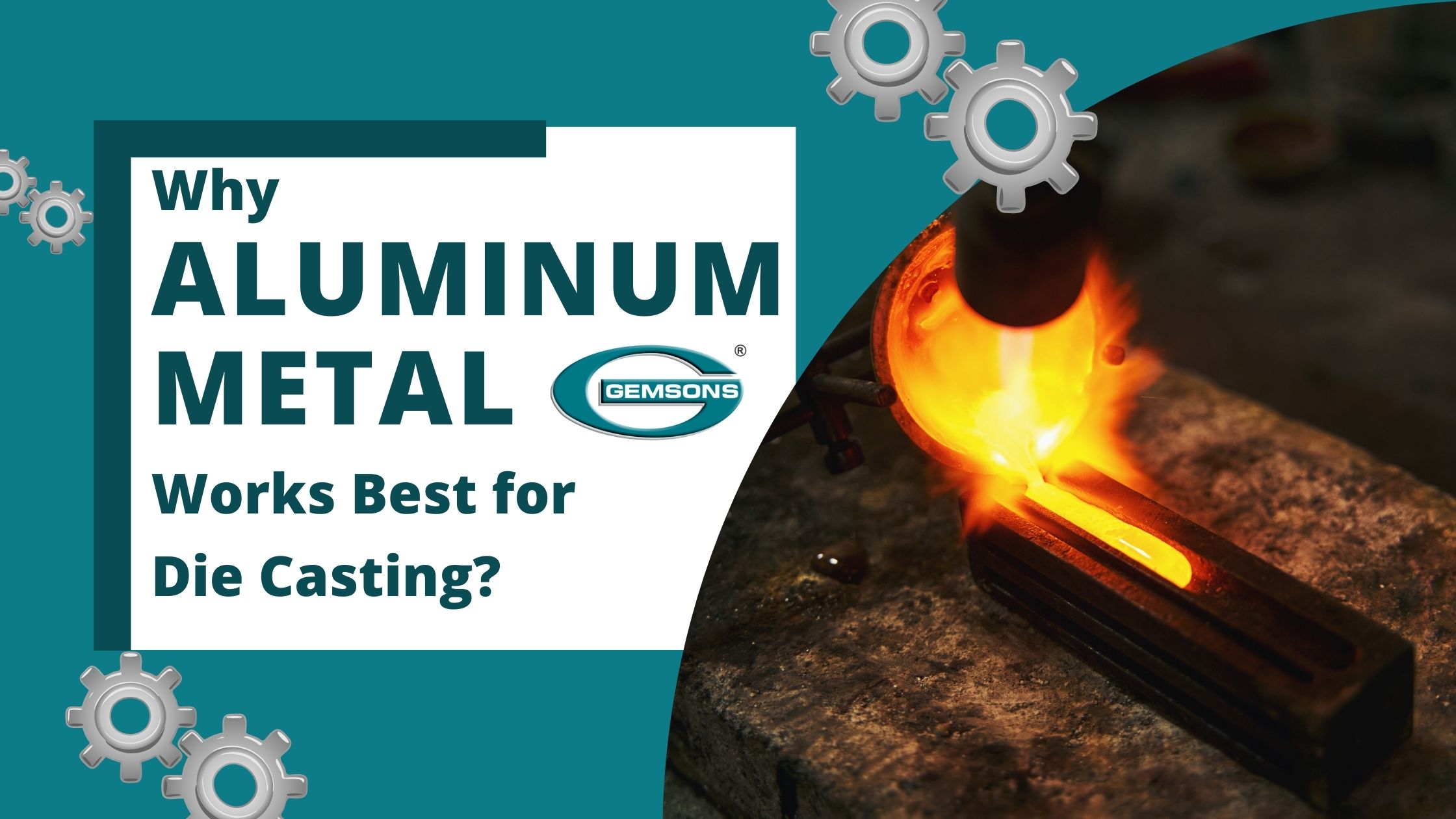
In precision spreading, 6063 is fit for applications where complex geometries and high-quality surface area coatings are vital. Examples include telecommunication enclosures, where the alloy's superior formability enables streamlined and visually pleasing designs while maintaining structural integrity. In the Lights Solutions sector, precision-cast 6063 elements produce stylish and efficient lighting components that need intricate forms and great thermal Resources efficiency.
It causes a finer surface coating and much better deterioration resistance in A360. The A360 shows premium prolongation, making it ideal for complex and thin-walled parts. In accuracy spreading applications, A360 is fit for industries such as Customer Electronic Devices, Telecommunication, and Power Tools. Its enhanced fluidness permits detailed, high-precision parts like smartphone casings and interaction device real estates.
The smart Trick of Alcast Company That Nobody is Discussing
Its one-of-a-kind residential or commercial properties make A360 a valuable selection for accuracy casting in these markets, boosting product sturdiness and top quality. Light weight aluminum alloy 380, or A380, is a widely utilized casting alloy with a number of distinctive qualities. It uses excellent castability, making it an excellent choice for accuracy casting. A380 displays excellent fluidness when molten, making certain intricate and comprehensive molds are precisely reproduced.
In accuracy casting, light weight aluminum 413 beams in the Customer Electronics and Power Equipment industries. This alloy's superior rust resistance makes it a superb choice for exterior applications, guaranteeing durable, resilient items in the discussed sectors.
More About Alcast Company
When you have actually decided that the light weight aluminum pass away casting procedure appropriates for your project, an important following step is selecting the most ideal alloy. The light weight aluminum alloy you choose will considerably impact both the spreading procedure and the buildings of the end product. As a result of this, you have to make your decision meticulously and take an enlightened approach.
Identifying the most ideal aluminum alloy for your application will certainly indicate weighing a wide selection of qualities. The very first category addresses alloy attributes that affect the manufacturing process.
Alcast Company Can Be Fun For Anyone
The alloy you choose for die spreading straight impacts several aspects of the spreading procedure, like exactly how simple the alloy is to work with and if it is susceptible to casting defects. Warm fracturing, also called solidification cracking, is a regular die spreading problem for aluminum alloys that can cause internal or surface-level splits or splits.
Certain light weight aluminum alloys are more at risk to warm splitting than others, and your selection must consider this. Another typical defect discovered in the die casting of light weight aluminum is pass away soldering, which is when the actors stays with the die walls and makes ejection hard. It can harm both the cast and the die, so you must look for alloys with high anti-soldering residential properties.
Rust resistance, which is currently a notable characteristic of light weight aluminum, can differ substantially from alloy to alloy and is an essential characteristic to take into consideration depending on the ecological conditions your product will certainly be subjected to (Aluminum Casting). Use resistance is another building frequently looked for in aluminum items and can distinguish some alloys